5 Workplace Safety Risks and How Small Businesses Can Mitigate Them
ByJulian Gette
Workast publisher
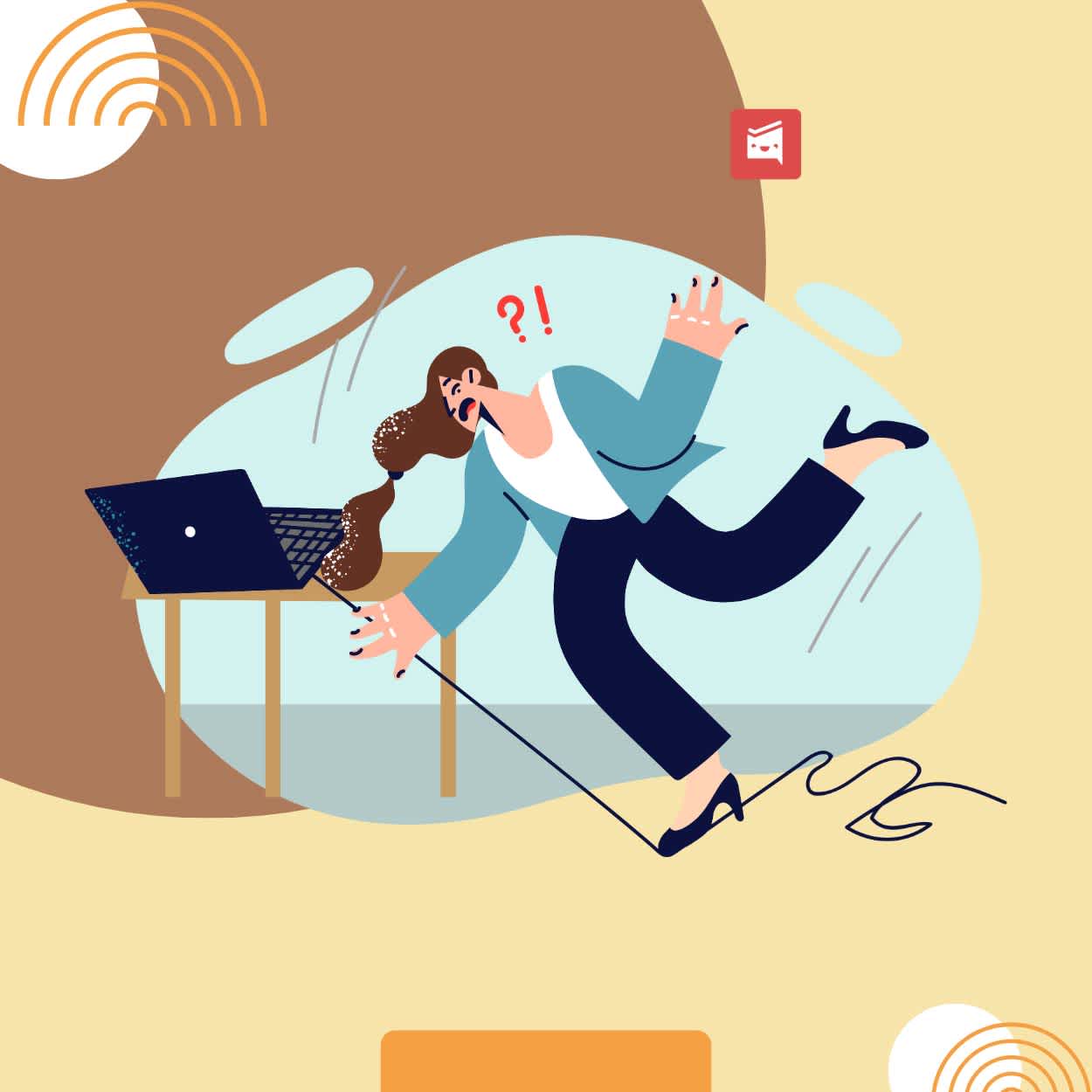
Workast publisher
In the original Divine plan, work was a privilege and a blessing. The world was so arranged that work was necessary and good. Though this is still true, equally so is the fact that some jobs are more dangerous than others.
By this, we mean that certain professions carry a greater risk of injury or even death. Some of the most dangerous jobs in the world include those of logging workers, firefighters, flight engineers, truck drivers, and construction workers.
Studies have found that nearly 3 million people die due to occupational accidents or hazards every year. Additionally, around 395 million sustain non-fatal injuries. Even small business employees are at risk of occupational accidents.
Even if a company hires two to five employees, it is the employer’s responsibility to offer a safe working environment. In this article, we will discuss the five most common workplace hazards and ways in which small businesses can ensure worker safety.
First, let's look at the five most commonplace workplace hazards that companies must be careful of.
These hazards typically refer to any type of threat present in the workplace environment. In general, physical hazards would involve extreme weather conditions that make the environment unfit for working.
This means if employees are at risk of radiation, ultraviolet sun rays, frost bites due to snow, etc, they are facing physical hazards. Besides these, even loud noise can become a hazard.
According to the Occupational Safety and Health Administration (OSHA), hearing conservation programs are a mandate. Employees will be exposed to noise levels of 85 decibels or more for 8 working hours.
The Centers for Disease Control and Prevention (CDC) states that chemical hazards in the workplace can take several forms. It may include any type of chemicals found in their solid, liquid, or gaseous state that are particularly toxic to the body.
A prime example would be per- and polyfluoroalkyl substances (PFAS) used heavily by the firefighting industry. These carbon-fluorine chemical compounds are used to manufacture Aqueous Film Forming Foam (AFFF) and lined in the turnout gear. According to data shared by TorHoerman Law, firefighters developed kidney, bladder, and testicle cancer due to regular exposure to PFAS.
This is precisely why over 7000 of them filed an AFFF lawsuit to seek justice. Veterans from this list are also eligible to apply for a VA claim for compensation. Similarly, aerosols and particulate matter pose a major threat to workers.
This type of workplace hazard generally refers to disease-causing agents that may be present in the working environment. They can be easily transmitted from one individual to another through various modes of transmission. Regular exposure to biological hazards can cause acute or chronic health conditions.
Examples of these hazards would include toxins, pathogens, spores, etc. Biological hazards can mostly be found in hospitals, waste collection facilities, and grain-producing factories.
These hazards make up the most common form of occupational risk. They often involve a mishap that can be associated with a specific job role. For instance - a construction worker is at risk of falling from a height or getting under heavy machinery.
Other forms of workplace safety hazards include spills, electrocution, tripping over obstacles, and more.
The final category of occupational hazard to be careful of has to do with a worker’s mental health. There may be a variety of workplace stressors that have long-term effects on an employee’s psychological well-being.
Examples of psychosocial hazards would include extreme workload demands, micromanagement, discrimination, or harassment. A positive work culture is of utmost importance for a healthy workforce.
We have just discussed the five most common risks or hazards workers are vulnerable to, even those working for small businesses. Now, let's look at how companies can handle or mitigate such risks.
No business, large or small, is capable of mitigating workplace safety risks unless it knows them properly. So, the first step to keeping your workplace safe is to conduct a risk assessment.
Here, you must determine which hazards are most likely to affect your workers - chemical, biological, etc. Then, identify which specific risks would cause the most harm. For instance, find out the chemicals or pathogens that are mostly found in your workplace.
Any identified risks must be communicated to all levels of the organization. If there are any injuries or illnesses, these must be identified and reported. Regular inspections may be required to keep track of any new or recurring hazards.
Employee training in all aspects, especially workplace safety, has several benefits. Studies have found that businesses that invest in training sessions are likely to earn 218% higher income than those that don't.
Moreover, employees tend to feel more engaged as they find better opportunities for career advancement. To run a successful employee safety training program, small businesses need to identify the most common risks within their scope of work.
Then, they must conduct training sessions for all organizational levels in line with any policy or procedural changes. The sessions can be a mix of theoretical knowledge and in-person training for 360-degree knowledge.
The interesting thing is that workplace safety laws tend to evolve. Small businesses that do not keep up with the changing standards will fail to maintain a safe work culture.
It is crucial to review all safety policies at least once a year for compliance. Once the review process is done, the health and safety committee must be notified of any changes in procedures, equipment, physical locations, and more. This will not only keep everyone on the same page but will also help reduce costs.
Lastly, keep in mind that occupational injuries of any kind are extremely costly for your workers and your small enterprise. As per the data shared by Statista, overexertion due to external sources accounts for the highest costs, amounting to $12.49 billion on average each year.
This is closely followed by fall accidents, being struck by equipment, and roadway incidents. Such tragedies do not spare small businesses that may already be facing a capital crunch. So, it is best to plan and create a safe work environment as far as possible.